The food industry has a range of solutions that combine performance and sustainability. Industrial heat pumps are emerging as a key technology for optimising thermal processes such as sterilisation and pasteurisation. This equipment helps to reduce dependence on fossil fuels used in industrial boilers, by recovering waste heat to reduce the energy cost of installations and improve their COP.
Chillers, which already have a strong presence on the market, can be used in architectures with heat pumps. They limit the refrigerant charge while guaranteeing optimum thermal efficiency, offering a relevant compromise between efficiency, regulatory compliance and durability.
To take the decarbonisation of the agri-food industry one step further, the choice of heat transfer fluid for the secondary circuit also plays a crucial role. While several solutions exist to meet the needs of secondary circuits, not all are equal.
Greenway® Neo N, produced by Climalife, is the ideal alternative to fossil-based glycol heat transfer fluids such as MPG or MEG. This bio-sourced 1,3-propanediol-based heat transfer fluid is NSF HT1 registered and non-harmful.
Environmental approach: life cycle analysis
Formulated from bio-sourced 1,3-propanediol, its production has a much lower carbon impact than MPG. CO2 emissions are down by 84%, and energy consumption is down by 70% on a like-for-like basis.
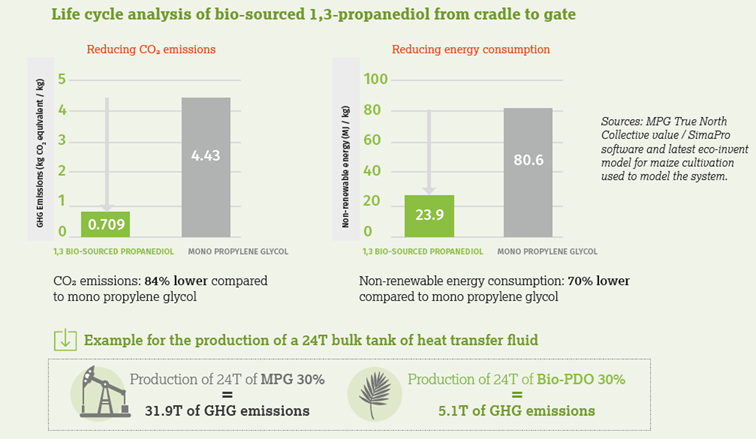
Greenway® Neo N, the ideal heat transfer fluid for the food industry
Thanks to its low viscosity, Greenway® Neo N can be used at very low temperatures compared with traditional MPGs, and therefore increases productivity. It also makes it possible to reduce the size of pumps and piping, thereby cutting installation and operating costs.
This solution is also advantageous for hot processes such as sterilisation and pasteurisation. When used in a high-temperature loop circuit, Greenway® Neo N offers greater stability and better resistance up to 200°C, compared with other glycol-based products which degrade at around 150°C.
Choosing a bio-sourced heat transfer fluid such as Greenway® Neo N combined with a refrigerant with a very low GWP helps to reduce the environmental footprint of a facility and decarbonise the food industry.