Europe is striving to be the world’s first climate-neutral continent by 2050. This statement paves the path for a lot of effort, regulation, innovation and change that European people and industries have to go through.
Building a better future for society through climate neutrality is a great opportunity but one that is also full of challenges. Economic sectors like transportation, buildings, agriculture and industry will play a significant role to reach that goal. Europe’s next milestone is to decrease CO₂ emissions by 90% in 2040 compared to 2019 levels and that is not an easy one.
We all know about electric vehicles and how superior they are compared to the conventional ICE (internal combustion engines) when it comes to energy efficiency, electric motors are simply three times more efficient compared to combustion engines and that is the prime reason behind their fast adoption in the past decade.
We also know why certain technologies, such as photovoltaic solar energy or electricity generation using wind power are superior to the conventional way of generating electricity through fossil powered power plants.
One can argue that the same applies to every new technology before the market fully embraces it, it is better, but it might seem more expensive at first glance.
The European Industry today contributes to roughly one third of the EU’s final energy demand and about 20% of the total GHG emissions in Europe.
If you get to look at any industry today the requirement for energy can be classified into 2 categories:
- Electricity to power the production lines, machinery and provide light as well as enabling the cooling and refrigeration equipment to contribute to the industrial process.
- Fossil fuel to power industrial boilers which generate either hot water, steam or indirectly heat the air for processes like drying and baking.
In this article, we will focus on one technology and one industry to demonstrate how we can tackle the decarbonization opportunity one step at a time.
Heat pumps & Food and beverage industries
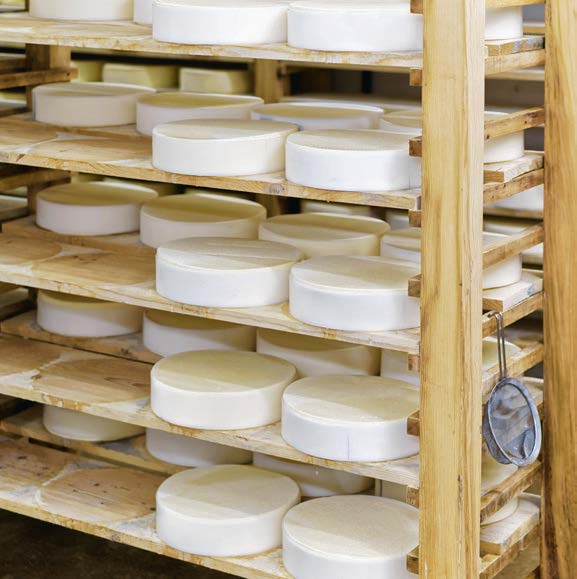
In the food and beverage industry the fossil to electricity ratio is about 80/20. Most of the fossil fuel used is to power industrial boilers which heat the process up to temperatures that rarely cross 150°C.
F&B is the lowest hanging fruit among all industries today, it is one of the easiest industries to be decarbonized today due to the presence of industrial heat pumps which can easily replace or minimize the dependency on fossil fuel boilers. Each member state has hundreds if not thousands of factories that provide food and beverages to the people as well as export it to other countries.
Heat pumps are the EVs of heating; they do not only provide sustainable heating and end the reliance on gas boilers, but they can be harnessed to provide cooling if engineered and integrated the right way into a process.
Most readers know how 10 KW heat pumps can replace boilers at home to provide hot water at 55°C in a very efficient way that can provide a very short return over investment and financial savings, but not many know how it can work in an industrial facility to provide hot water or steam up to 150°C. Every industrial process emits waste heat that is emitted to the atmosphere, think condensers for a refrigeration system, cooling towers, CHP plants and flue gas, most of those represent a perfect heat source to an industrial heat pump on an industrial scale.
For instance, when you harness waste heat at 50°C and lift it using a heat pump to 100°C then you have a coefficient of performance (COP) of 4.5 using R-1233zd(E). This means that you can be almost 500% more efficient than a conventional industrial gas boiler.
This example can minimize or eliminate the use of fossil fuel, cut CO2 emissions, provide the process with the heat needed to produce the end product while saving on OPEX at the same time.
There are tens of processes that can benefit from Industrial heat pumps today like sterilization, pasteurization, cooking, drying, brewing, distillation, blanching and many others within the F&B industry.
The extra bonus of using heat pumps is that you can get cool out of them as well, which can help meet the process cooling needs and reduce the consumption of existing process chillers.
Refrigerants
People often know the working principle behind heat pumps, a working fluid (refrigerant) absorbs the heat from one side (heat source), then it gets compressed by a compressor to elevate its pressure and then heat is rejected on the other side (heat sink). However not all heat pumps are the same.
There are many aspects that get overlooked and one of them is the selection of the working fluid (refrigerant). There are different aspects that have to be considered before choosing the refrigerant for your application:
- GWP* and ODP*.
- Safety class (from non flammable, non toxic to highly flammable and highly toxic).
- Operating envelope (Boiling and critical temperature).
- Operating pressure.
- Volumetric heating capacity.
- Efficiency.
For industrial heat pump applications the main refrigerants that are used are:
- Ammonia: Very low GWP, classified as B2L which means that it’s slightly flammable but it is highly toxic at very low concentrations.
- Hydrocarbons (Butane, Pentane, Isobutane, Isopentane): Very low GWP, combine good heating capacity and efficiency but highly flammable and explosive (A3).
- HFOs (Hydrofluoro-olefins): The 4th generation of fluorinated gases, very low GWP & ODP, each HFO is engineered for specific use with a spectrum of different thermodynamic and safety properties. Some of the most popular ones that are used in industrial heat pump applications are R-1234ze(E) & R-1233zd (E) under the brand Solstice® from Honeywell.
- Water: This is arguably the one refrigerant that is used solely for steam generation or steam recompression.
The importance of safety
Safety plays a huge role in any industrial process, there is a big difference when you operate a heat pump for a single-family home where the charge of the refrigerant does not exceed 200 grams versus operating a heat pump for an industrial process where the refrigerant charge starts from 50 kg and can go up to thousands of kgs. In a real world where leakages can happen things can get extremely out of hand if the refrigerant used is toxic and operating under 80 barg or is highly flammable and explosive in an environment that has an explosive hazard like spirits distillation, sugar mill, paper and pulp plant. The example above shows that heat pumps can help to decarbonise the food industry. Certain types of refrigerant present risks, unlike those classified as non-toxic and non-flammable, which can be extremely efficient and safe in an installation.
Final thoughts
Heat pumps can play an instrumental role in the decarbonization of light industry in Europe to accelerate the NZE (Net Zero Emissions) goals.
The technology is ready and many member states provide different types of subsidies, funds and grants to support the industry in the initial investment as well as the running costs, Heat pumps are a viable option for industries that have an existing CHP (combined heat and power) plant to produce their own electricity as well as members states that have an electricity to gas price ratio of (Heat pump COP – 1).
Example: If the heat pump has a COP of 4 and the price of electricity to gas is 3 then the heat pump will be a viable option.
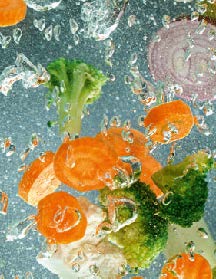
Choosing a non-toxic and non-flammable or mildly flammable refrigerant eliminates so many risks that industrial end users have to go through if they opt for a toxic or flammable refrigerant.
Finally, heat pumps can be a great solution to bring Europe’s industrial sector to be more competitive as it will enable the industry to have a much lower energy intensity for the end products, and thus decrease the energy cost burden and open the door for increasing the industry’s bottom line, offer more competitive pricing or even increase the production capacity and avoid bottlenecks.
* GWP: Global Warming Potential * ODP: Ozone Depleting Potential * OPEX: OPerational EXpense