Situé à Seclin dans le Nord de la France, le Leclerc drive s’est agrandi l’an passé et a robotisé la partie logistique / livraison de l’entrepôt pour mieux répondre aux attentes de ses clients tout en améliorant les conditions de travail de ses employés. Ce qui induit la mise en place de nouvelles installations frigorifiques pour le stockage des bacs de produits frais et des surgelés en attente d’être livrés. Le frais représente 35 % à 40 % des commandes.
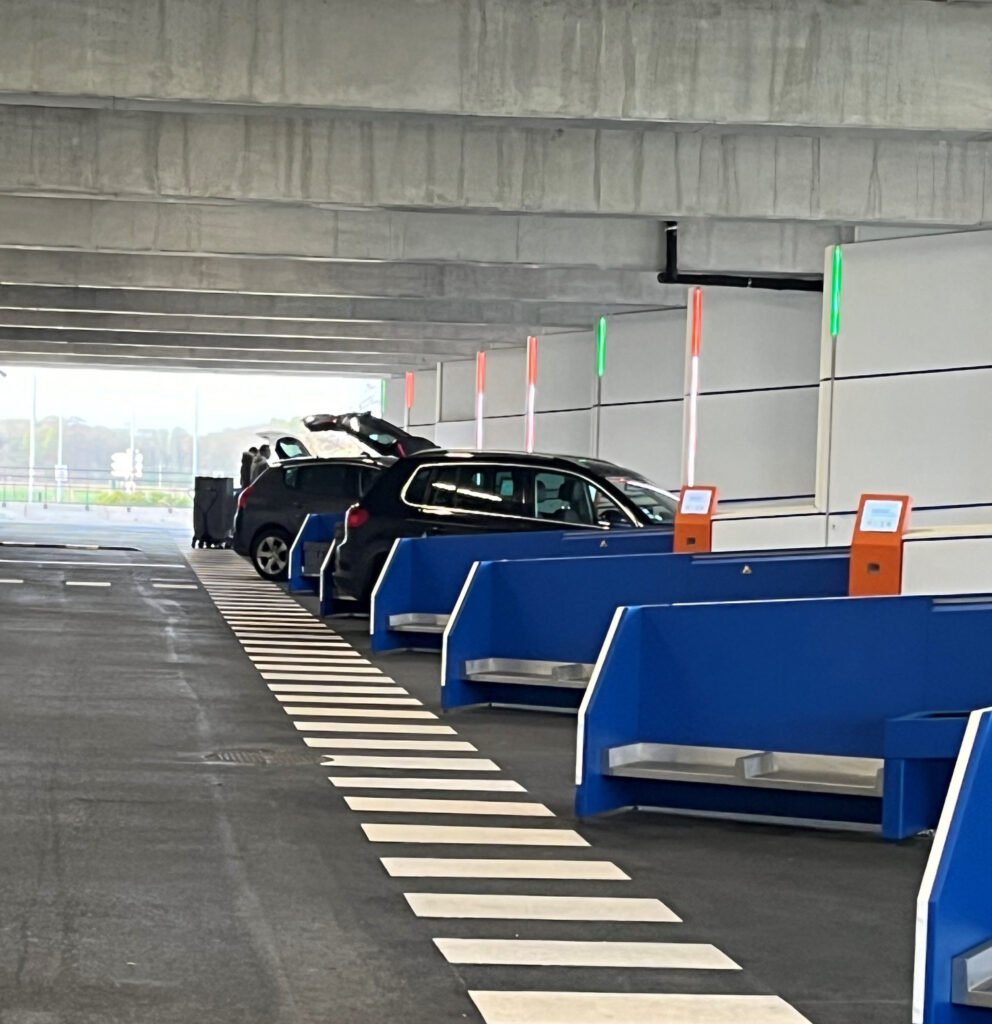
Installé en 2012 dans un bâtiment existant, le Leclerc drive décide de poursuivre son développement dix ans plus tard en triplant sa surface de stockage pour la porter à 5000 m². Avec une nouvelle conception en étage et la mise en place d’une automatisation partielle du processus de picking, le nouveau système permet de proposer plus de 15 000 références et de préparer plus de 150 commandes par jour dans un temps record.
L’objectif est de toujours mieux répondre aux attentes des clients avec une livraison dans les plus brefs délais et sur des plages horaires plus étendues.
« Aujourd’hui, nous mettons à disposition la commande en 3 minutes contre plus de 5 auparavant. Et si le client commande après 16h, il peut être livré le jour même dès 18h. Nous sommes maintenant ouverts de 8h à 20h30. Avant nous devions fermer des créneaux afin que le personnel puisse préparer les commandes » nous explique Quentin Tronel, directeur du Leclerc Drive.
Cette robotisation permet aussi de réduire la pénibilité et la fatigue des employés même si la zone de picking n’a pas changé de place. Grâce au nouveau système, l’organisation est modifiée et chaque opérateur s’occupe dorénavant d’une zone bien définie. Il peut ainsi ramasser 20 commandes en une seule fois, alors qu’auparavant de nombreux allers retours étaient nécessaires.
Les 70 collaborateurs bénéficient en outre d’une journée de repos supplémentaire et travaillent maintenant 5 jours sur 7.
Un projet d’envergure pour ce nouveau système “ Made in France ”
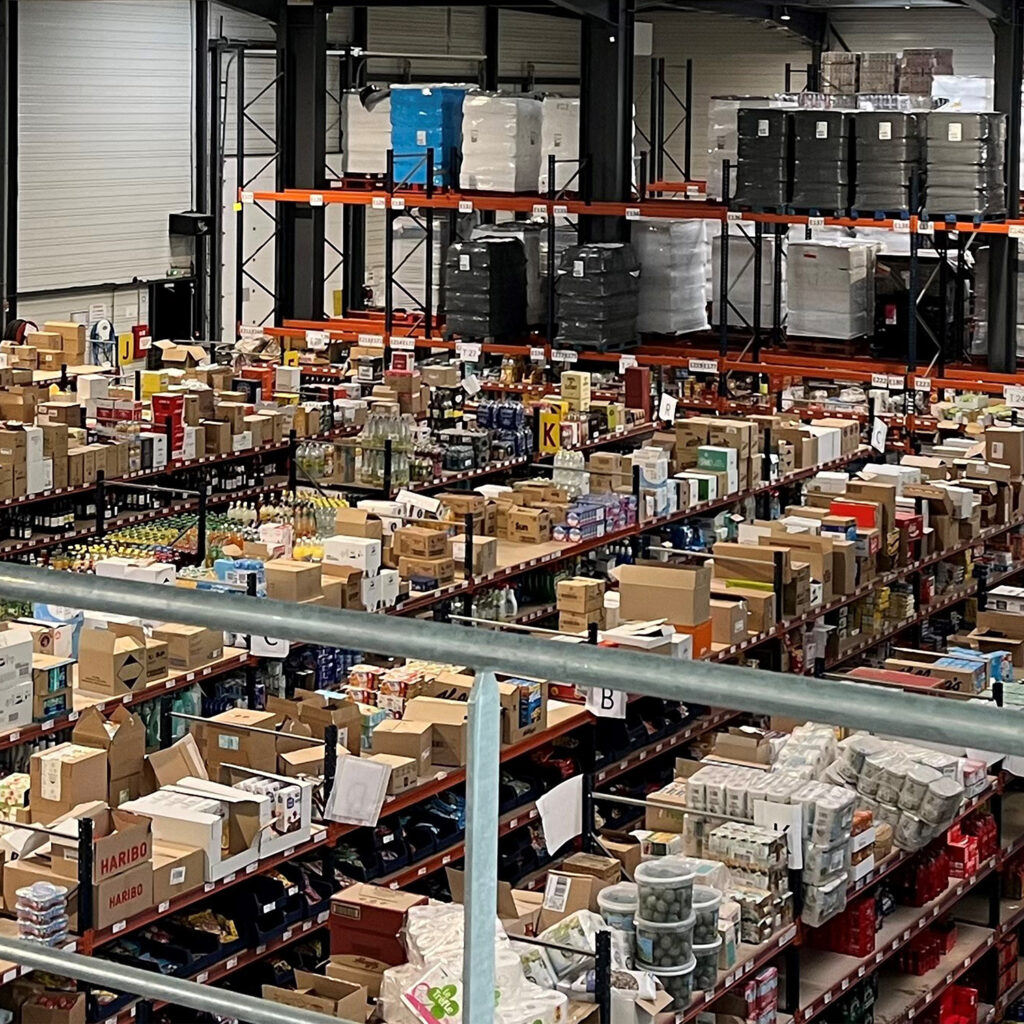
Le chantier de 7 millions d’euros a requis plus d’un an et demi de travaux et quatre mois de tests pour aboutir à une utilisation à 100 % du process en mars 2023. Il s’agit du septième drive automatisé en France mais le premier avec ce nouveau système.
Le projet est découpé en plusieurs phases avec notamment la construction d’un nouveau bâtiment accolé à l’ancien en y intégrant un étage. Pour la partie réfrigération, Leclerc fait appel à la société Thélia, partenaire de confiance depuis de nombreuses années. Six mois d’intervention seront nécessaires pour concevoir et implémenter les nouvelles installations frigorifiques.
Le choix du R-455A pour sa fiabilité et sa simplicité de mise en oeuvre
Très rapidement, Pascal Lejeune, Directeur technique du drive, écarte la solution CO2 pour les nouvelles chambres froides (500 m² pour le positif et 60 m² pour le négatif). Il souhaite rester sur une technologie similaire à celle déjà en place actuellement pour le drive (R-449A) et pour l’hypermarché Leclerc dont il a aussi la charge. Jérôme Goetz, dirigeant de l’entreprise Thélia, préconise alors de passer sur un fluide frigorigène de long terme avec des groupes modulaires pour sécuriser la production de froid. Le choix se porte sur le R-455A qui permet une charge plus importante que le R-454C. C’est une solution fiable, sûre et accessible pour l’ensemble des techniciens avec des coûts d’investissement plus avantageux.
Trois groupes de condensation de marque REFRA distribués par Fritec sont installés en toiture du nouveau bâtiment. Deux groupes de 7 kW alimentent la chambre froide négative avec chacun une charge de 14,8 kg de R-455A. Le troisième de 18,5 kW alimente un SAS et deux évaporateurs de la chambre froide positive située à l’étage avec une charge de 19 kg.
Un quatrième groupe REFRA de 61 kW est placé à l’extérieur du bâtiment pour compléter la production de froid de cette chambre froide positive de 500 m² et alimenter le nouvel évaporateur Kelvion installé dans la chambre froide existante du rez-de-chaussée suite à l’agrandissement de celle-ci. Le tout est équipé d’une détente thermostatique et des détecteurs à poste fixe ont été mis en place pour garantir la sécurité des personnes.
« La mise en place du Solstice® L40X a permis de démystifier ces fluides légèrement inflammables auprès des techniciens. Une fois que le calcul de charge est réalisé, que nous avons défini les éléments de sécurité si nécessaire, on peut mettre en oeuvre le R-455A simplement » rappelle Jérôme Goetz.
La principale complexité dans ce projet ce n’est pas la technologie en tant que telle mais l’environnement dans lequel elle sera mise en place. Il faut avant tout gérer l’hygrométrie et le fait de ne pas pouvoir intervenir dans les chambres froides sans arrêt de l’automatisme.
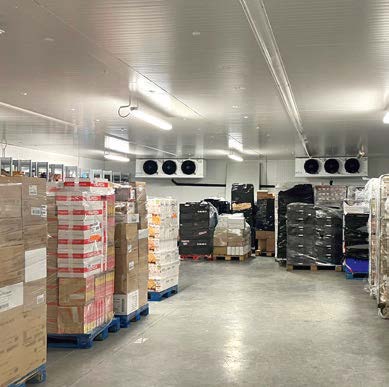
au rez-de-chaussée avec ajout d’un évaporateur Kelvion.
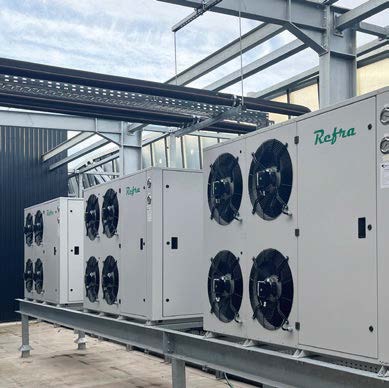
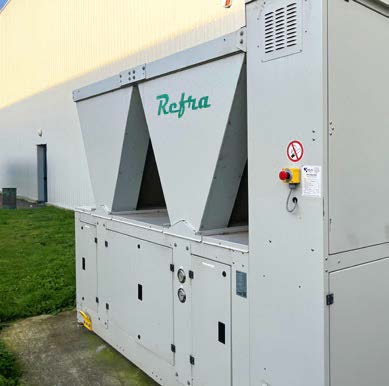