Located in Seclin in northern France, Leclerc Drive expanded last year and automated the logistics/delivery section of its warehouse to better meet customer expectations while improving working conditions for employees. This has led to the installation of new refrigeration facilities for the storage of crates of fresh produce and frozen foods awaiting delivery. Fresh produce accounts for 35% to 40% of orders.
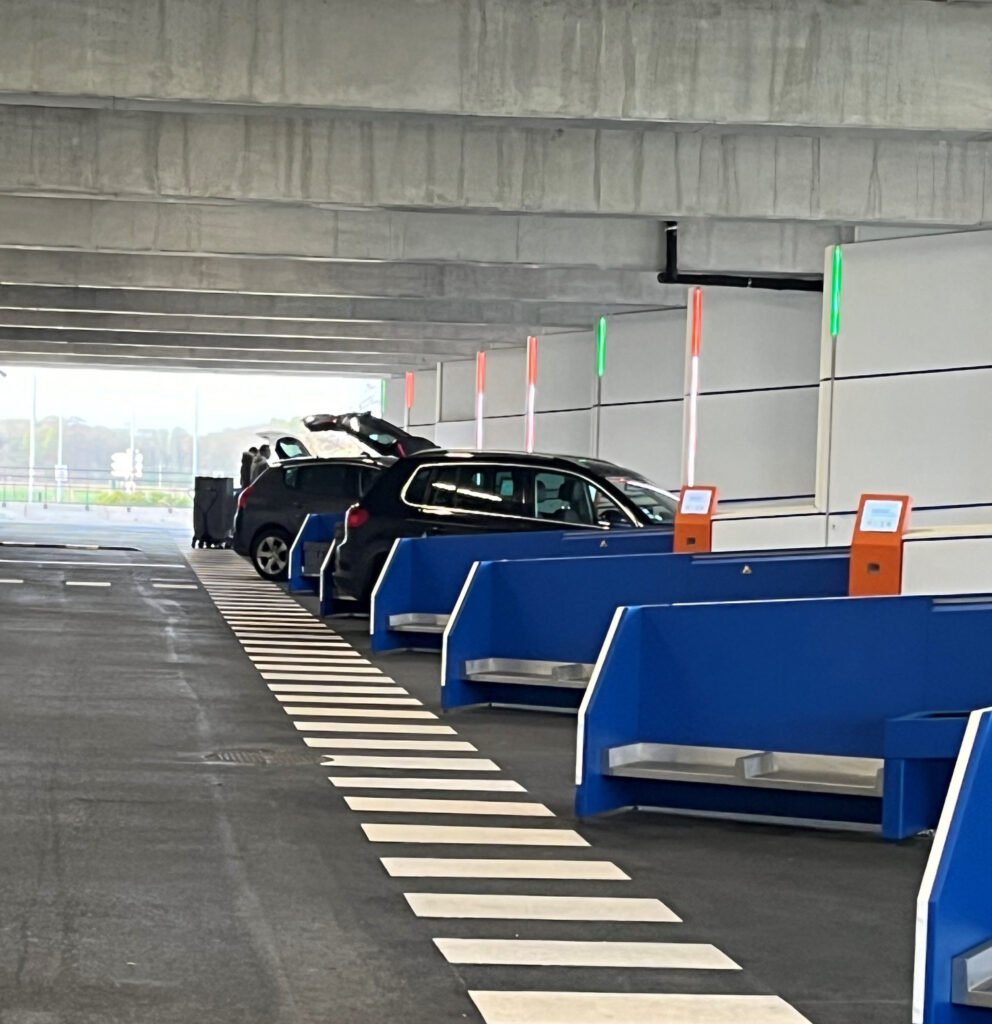
Installed in 2012 in an existing building, the Leclerc Drive decided to continue its development ten years later by tripling its storage area to 5,000m². With a new multi-storey design and the introduction of partial automation of the picking process, the new system makes it possible to offer more than 15,000 products and prepare more than 150 orders a day in record time.
The aim is to meet customer expectations even more effectively, with quick delivery over longer opening hours.
“Today, we create orders within 3 minutes, compared with over 5 minutes previously. And if customers order after 4pm, goods can be delivered the same day from 6pm. We are now open from 8am to 8.30pm. Before, we had to close during certain time slots so that staff could prepare orders,” explains Quentin Tronel, Leclerc Drive manager.
Automation also makes it possible to reduce employee fatigue, even though the picking area has not changed. Thanks to the new system, the organisation has changed, and each operator is now responsible for a clearly defined area. As a result, they can pick 20 orders at a time, whereas previously they would have had to make numerous return trips.
The 70 employees also benefit from an extra day’s rest and now work five days a week.
A major project for this new “Made in France” system
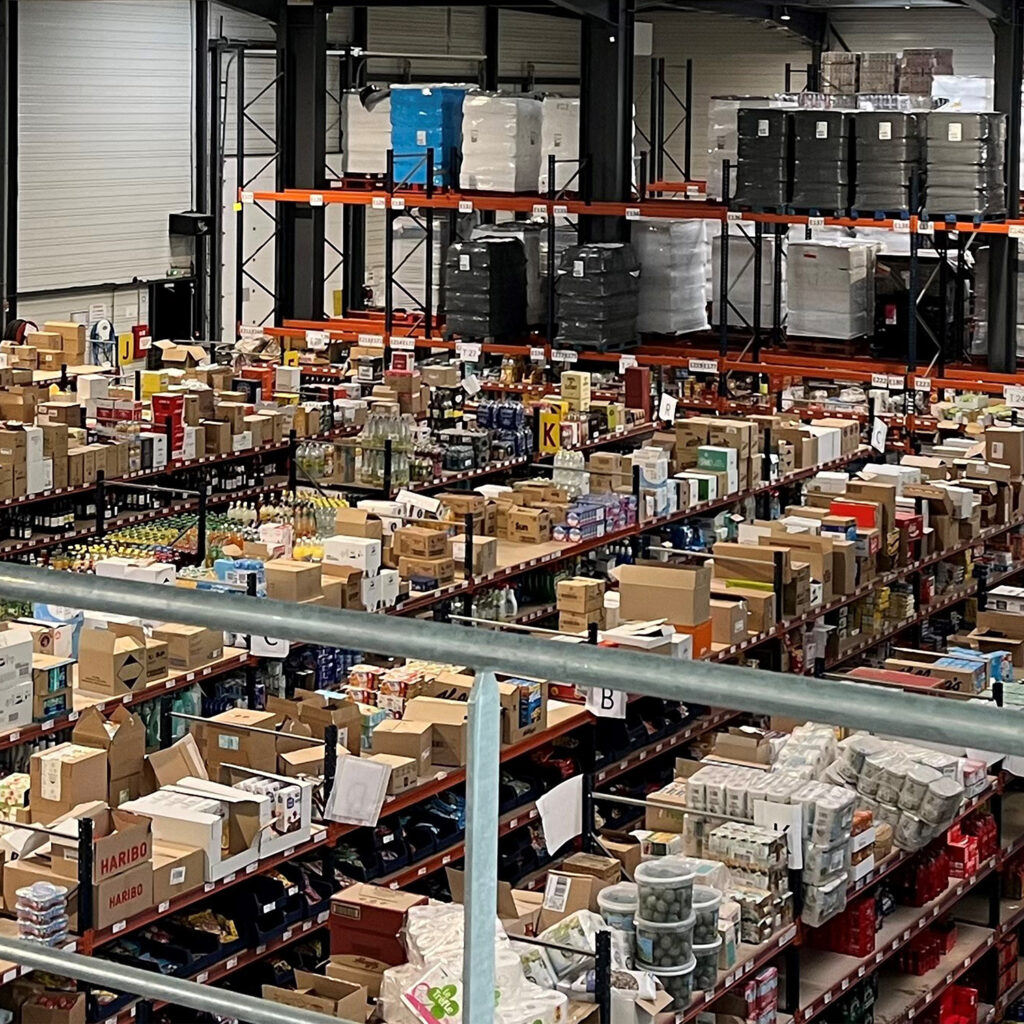
The €7 million project took over a year and a half to complete and four months of testing, culminating in 100% roll-out by March 2023. This is the seventh automated Drive in France, but the first with this new system.
The project was divided into several phases, including the construction of a new building adjoining the old one, with the addition of an upper floor. For the refrigeration part of the project, Leclerc called on Thélia, a trusted partner for many years. It took six months to design and implement the new refrigeration system.
Choosing R-455A for its reliability and ease of use
Three REFRA condensing units distributed by Fritec were installed on the roof of the new building. Two 7 kW units supply the low temperature cold room, each with a charge of 14.8 kg of R-455A. The third, rated at 18.5 kW, supplies an airlock and two evaporators in the medium temperature cold room on the upper floor, each with a 19 kg charge
Pascal Lejeune, Drive’s Technical Director, quickly ruled out CO2 for the new cold rooms (500 m² for chilled produce and 60 m² for frozen produce). He wanted to stick with a technology similar to the one already in place for Drive (R-449A) and for the Leclerc hypermarket, for which he is also responsible. Jérôme Goetz, head of Thélia, recommended switching to a long-term refrigerant with modular units to ensure reliable cooling. R-455A was chosen as it could handle a larger charge than R-454C. It is a reliable, safe and accessible solution for all technicians, with lower investment costs.
A fourth 61 kW REFRA unit was installed outside the building to complete the cooling production of this 500 m² medium temperature cold room and supply the new Kelvion evaporator installed in the existing cold room on the ground floor following its extension. The whole system is equipped with a thermostatic expansion valve, and fixed detectors have been installed to guarantee personal safety.
“The introduction of Solstice® L40X has demystified these mildly flammable refrigerants for technicians. Once the charge calculation has been carried out, and we’ve defined the safety elements, if necessary, it’s easy to implement R-455A,” explains Jérôme Goetz.
The main challenge in this project was not the technology as such, but the environment in which it had to be installed. Above all, we have had to manage the hygrometry and the fact that we can’t work in the cold rooms without stopping the process.
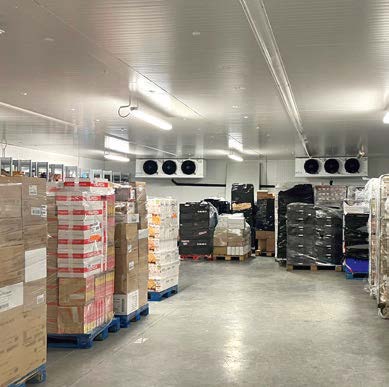
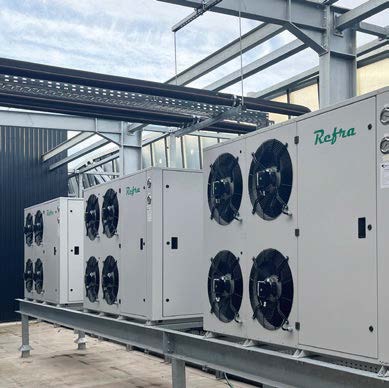
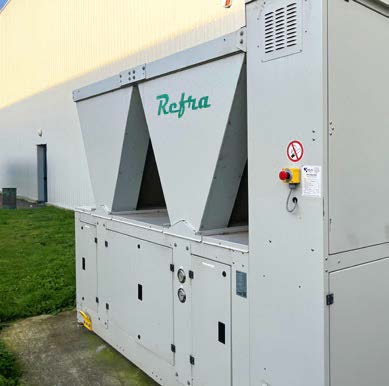