Interview with Fabien Marée, expansion agent specialist in the Development & Application / Technical Support department at Climalife.
In a context of sustainable development, what are the challenges in terms of insulation?
F. M.: Energy is vital to the global economy. Although energy efficiency standards are evolving to ensure quality of life and environmental friendliness, a significant amount of energy is still lost due to poor insulation. Insulation conserves the energy produced by a refrigerator, air conditioning and many other appliances. It limits heat transfer between the outside and inside. Good insulation therefore requires high thermal resistance and the lowest possible Lambda (thermal conductivity).
R = thermal resistance (the ability of the thermal insulation to resist cold and heat).
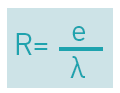
e = thickness λ = thermal conductivity
There are several types of insulation materials on the market, including synthetic insulation materials such as polyurethane and polystyrene foams. For good thermal performance, it is essential to choose the right blowing agents.
Can you explain why in more detail?
F. M.: Blowing agents are essential components in the manufacture of insulating foams. For decades, the majority of insulation boards have been produced from saturated hydrocarbons, such as n-pentane, cyclopentane or isopentane with a lambda between 12 and 15 mW/mK and a rather cheap price positioning. The arrival of new HFO (Hydrofluoro-Olefin) molecules makes it possible to go further and offer non-flammable blowing agents with better thermal conductivity. These molecules also have the advantage of having an ultra-low GWP like hydrocarbons. HFO 1336mzz, for example, has a Lambda of 10.4 mW/mK at 20°C and that of HCFO 1233zd is 10.2 mW/mK at 20°C. The latter has a real advantage in terms of thermal conductivity but not only that. It is also compatible with stainless steel, copper, brass, aluminium and other metals commonly used in polyurethane equipment and storage. Specifically, expansion agents with the lowest possible Lambda should be favoured to ensure better energy efficiency and avoid heat loss. It is ineffective and expensive to produce energy (hot or cold) without being able to use it.
In view of the energy crisis that is currently looming and will continue for years to come, one can imagine that the players in the polyurethane foam market have an interest in these new HFO solutions?
F. M.: In my opinion, there are two major interests in these new molecules. The first, as I mentioned earlier, is that it makes it possible to have more efficient insulation panels and to obtain a greater usable volume, whether for a cold room or a refrigerator, but also for the insulation of buildings, because the thickness of the foam is reduced. The second interest is to be able to meet the next regulatory ban coming into force on 1 January 2023. Indeed, the use of fluorinated greenhouse gases, HFCs, will be banned in Europe under F-Gas II if their GWP is greater than 150. HFOs are therefore alternative solutions to re-place HFCs used in many applications. In the building sector, for example, the HFC 365mfc / 227ea (93/7) blend, which is one of the most common products for spray polyurethane foam, could be replaced by HCFO 1233zd or HFO 1336mzz. Furthermore, it can be seen that some manufacturers of household appliances have al-ready switched to these new molecules. This is notably the case with refrigerator manufacturers who have replaced cyclopentane with the HCFO 1233zd molecule for its lower Lambda, which also allows them to increase the usable volume of the refrigerator.
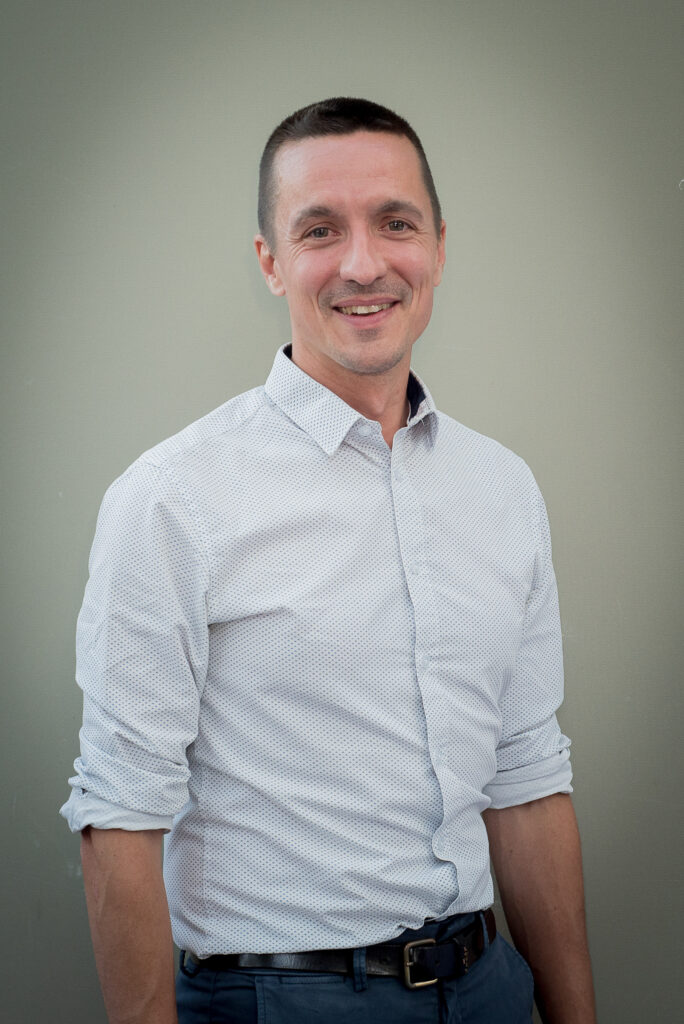
Insulation is not a factor to be ignored, it is necessary that each one of us, manufacturer, installer, end user, is aware of the improvements that can be implemented to reduce the carbon footprint and better respect our planet.
Fabien Marée, Climalife