One in four beers consumed in France is produced in Obernai, at the Kronenbourg Brewery, which employs over 600 people. Founded in 1664, Brasseries Kronenbourg became part of the Carlsberg group in 2008. The group has put
in place a policy to reduce its carbon footprint, cutting its CO2 emissions by 21% in three years by working on packaging, transport, water management and creating a responsible barley supply chain. Their catalogue includes over 30 brands and a growing number of alcohol-free products.
Refrigeration is a key factor in the production process. During the brewing process, after boiling, the mixture known as ‘wort’ is cooled to between 70 and 100°C. Fermentation then takes place, with yeast kept at a controlled temperature to control the process (taste, bitterness, alcohol
content). At the end of fermentation, the cold is also used to sediment the yeast at the bottom
of the tanks and facilitate the filtration process. Finally, the beer is transferred to a storage tank
and kept at 2°C until bottling.
Safety first
As part of a Group policy to improve the safety of facilities and people, Carlsberg decided to
convert all its breweries worldwide to non-toxic solutions by the end of 2024.
The objective was therefore to replace the MEG of the existing installation in one go during the
seven days of annual maintenance shutdown with four additional days, and not to exceed a residual MEG rate of 1%. This was a huge decision for the Obernai plant, for a number of reasons, including the size of the network, consisting of a single circuit, and the hundred or so people mobilised for the operation over 11 days. At the same time, despite the production stoppage, Trane chillers were hired to maintain the yeast at a controlled temperature.
The technical study was then entrusted to the Matal agency based in Strasbourg, a historic
region for beer production, with agency manager Emmanuel Keck, who is very familiar with
brewery environments.
The analysis of around 600 hours of engineering work focused on the choice of coolant, the
compatibility of valves and pumps with a new solution, and an estimate of the adaptations
required for optimal operation.
Friogel® Neo: the perfect solution
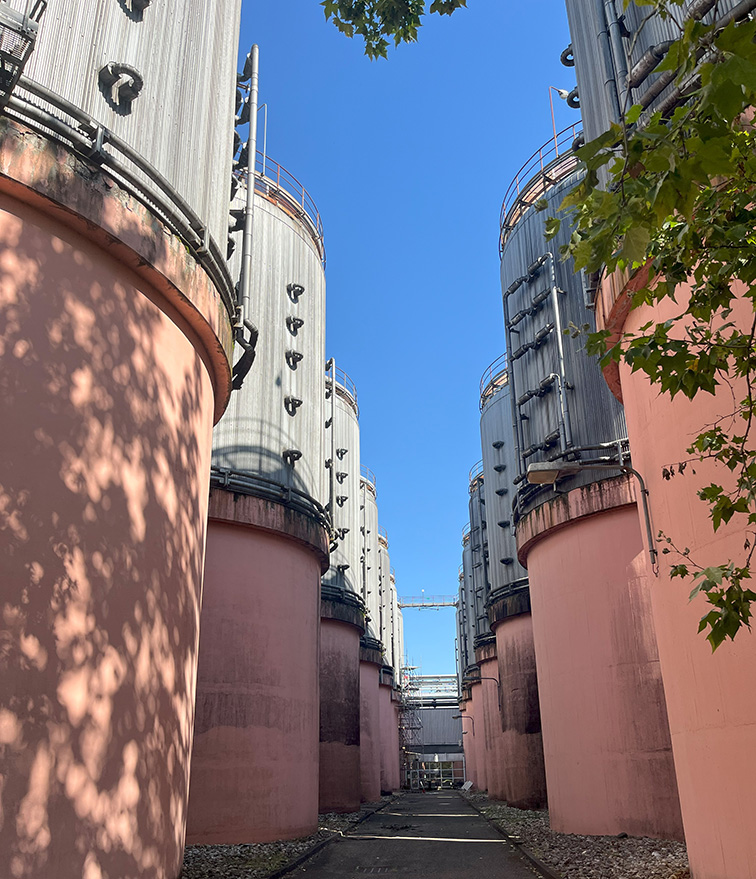
The plant dates back to the 1960s, and several extensions have been added over the years. It
has over 14 km of steel piping. It was important to choose a compatible solution carefully, so as
not to cause detachment of corrosion particles and to prevent clogging of filters and exchangers.
Several formulations were compared: salt-based, ethanol-based, bio-sourced 1,3-propanediol (Greenway® Neo N), and MPG-based with Friogel® Neo.
The latter was chosen because Friogel® Neo guaranteed miscibility, safety and better thermal
conductivity at a lower concentration, thus compensating for the difference in viscosity
between MEG and MPG and not consuming more energy for pumping.
Brasseries Kronenbourg chooses Climalife for turnkey service
Thanks to its two manufacturing plants and its logistics organisation, Climalife was able to supply the necessary quantities, as well as the human and material resources to recover and process the used product and refill it within the given timeframe.
After a preliminary inspection of the site and preparation of a prevention plan, the project was divided into several phases. A zone-by-zone organisation was defined to manage the automatic valves and the 500 purge points, a hundred of which were created specifically for the operation. The brewery made some of its staff available for the site, in order to retain control of the service, develop their team’s know-how and enable them to enhance their skills.
The Climalife and Brasseries Kronenbourg teams drained over 450 tonnes of the MEG network, which was transferred to temporary storage facilities rented for the occasion, for reprocessing at the Climalife plants.
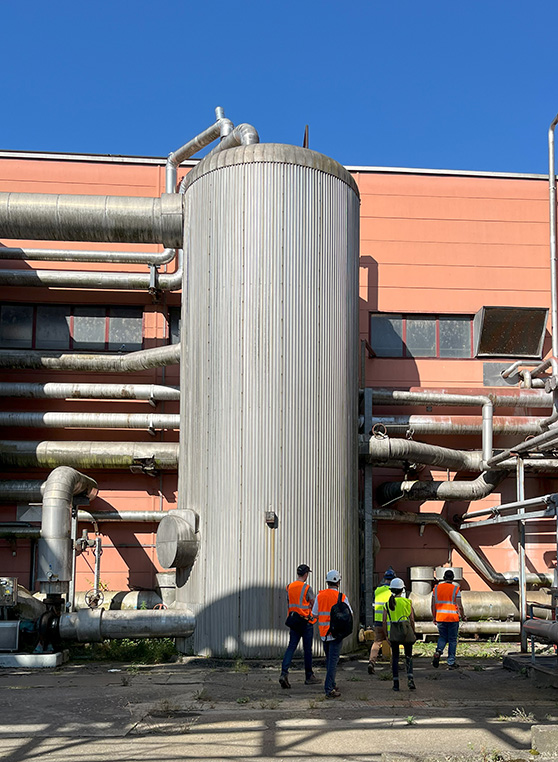
The rinsing operation was then carried out by Brasseries Kronenbourg’s technical services, along with tank cleaning and pipe repairs where necessary. For filling,
20 tankers were made available to deliver the 750 t of Friogel® Neo in bulk and store it before introducing it into the network.
The mission was successfully accomplished for this unusual transition in a short space of time. Climalife’s GPC analysis quantified the residual percentage of MEG in the system at 0.2%.
“And, no pumps, no piping, no plates in the exchangers were replaced. There were no changes to the recipe, and fermentation and production times are identical. It’s almost a dropin,” concludes Emmanuel Keck. Alain Christmann, Brasseries Kronenbourg Project Manager, also notes a slight reduction in energy consumption thanks to the improvements made.
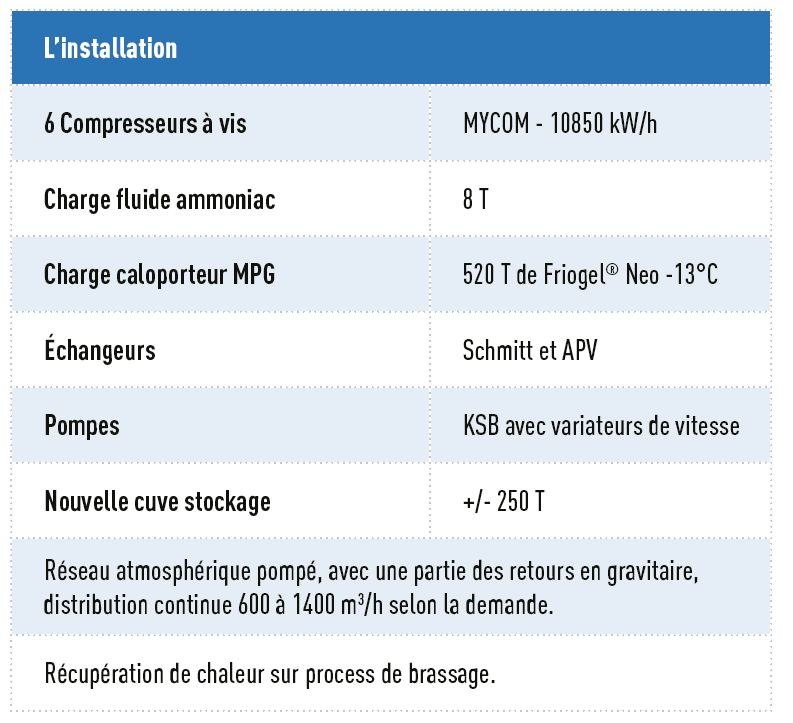
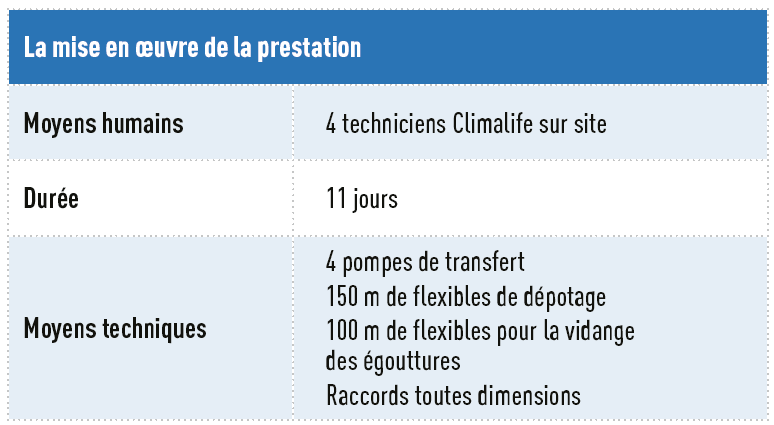
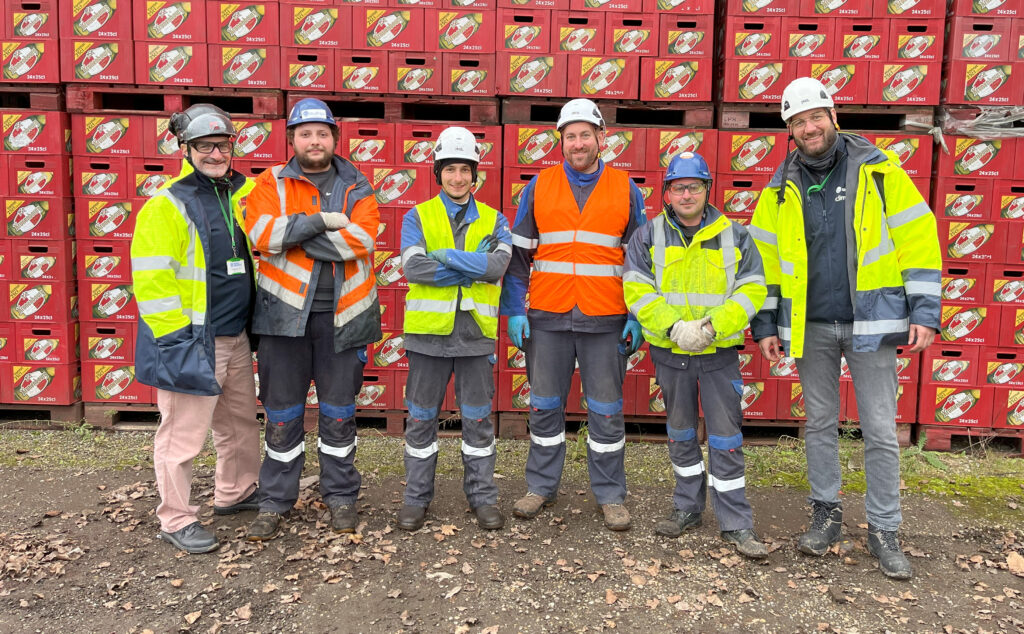
Mr Christmann, Brasseries Kronenbourg Project Manager, “particularly appreciated the Climalife team’s involvement on site and the coordination between
commercial and technical contacts”.