For 142 years, quality, creativity and the exclusive use of exceptional raw materials have guaranteed Maison Pécou’s reputation for excellence in the manufacture of dragées (a sugar coated sweet), by meticulously respecting the ideal conditions for manufacture as well as the drying times in dedicated spaces under controlled temperatures and humidity. At the end of the twentieth century, the recipe for the 70% cocoa chocolate dragée was created and was a huge success with consumers.
New chocolate specialities have recently been added to the range and the gourmet gift hamper business is growing strongly. The products are distributed mainly to wholesalers, party shops, delicatessens and national retailers. Located in Montauban (France), the family business achieved a € 6 million turnover in 2022 and employs 60 people.
Adaptation of cooling / heating processes
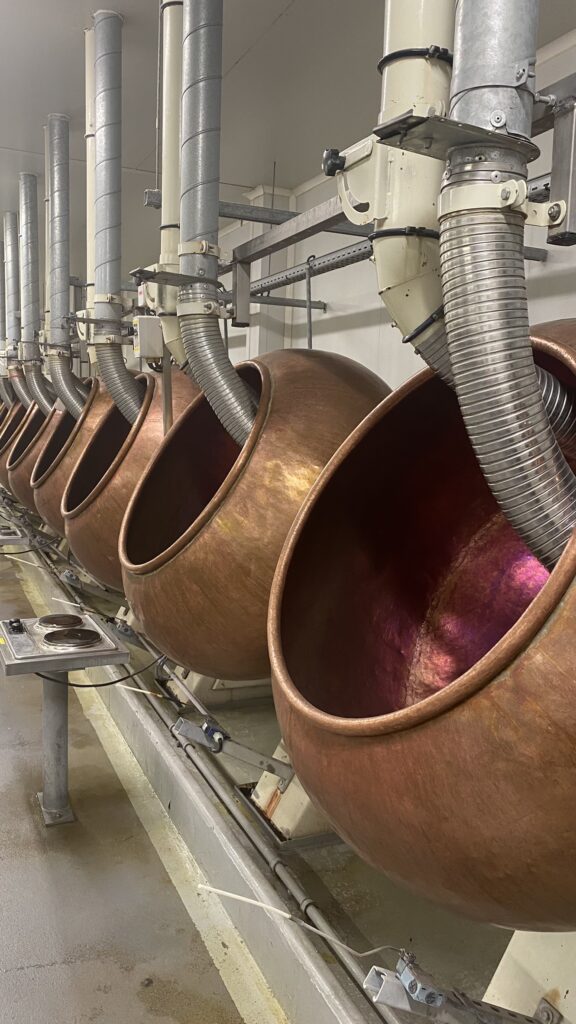
Since the opening of a new production site in 1972, the production workshop has continued to evolve. New spaces have been created or redesigned to switch from hot to cold.
« Traditionally, dragée was our business. To make this sweet product, we mainly needed to produce hot products. Over time, chocolate-based products have developed and our cooling needs have become increasingly important » explains Bernard Pécou, CEO.
The Pécou company has adapted its refrigeration needs, year after year, by adding independent direct expansion refrigeration systems, with supplementary electrical resistances for the heat supply, necessary for regulated humidity. This solution however was not ideal from an environmental point of view because of the disparity and characteristics of the refrigerants used and was no longer sufficient to meet their needs. It was necessary to completely redesign the site by renovating existing rooms, increasing their storage capacity, and improving the working conditions of the staff without forgetting the situation with greenhouse gases. In 2019, the company consulted various suppliers to discuss the project, and at the same time looked into its finance. It was not feasible for a SME of this size to invest without financial support.
Investment in a sustainable and optimised indirect system
Delzescaux, a company specialising in industrial and commercial refrigeration, decided to take part in this project with a technical solution adapted to their industrial process, financed in part by energy saving subsidies from EDF (French electricity supplier) for heat recovery. The support provided by Xavier Delzescaux, the company’s director, and his colleague Pierre Delpech, head of the design office, was greatly appreciated by Maison Pécou, which entrusted them with the project. « It was essential to us to offer a simple, centralised refrigeration system that could be adapted for the years to come, using refrigerants with a very low environmental impact, and to recover all the heat to optimise energy consumption and use it in their process » explained Xavier Delzescaux. Estimated at € 1 million, the project was 40% financed by energy saving certificates and other regional subsidies to support the economic development of the food production sector and as part of a CSR programme.
A site disrupted by Covid
The requirements were clearly defined. Pierre Delpech explains: « Within the new extensions at the 5,500 m² site, 1,760 m² had to be equipped for cooling, heating and humidity control, with the heating part representing 650 m² and the relative humidity 175 m², ». The construction began in July 2020, running in parallel with existing installations so as not to interrupt production. It took nearly two years due to supply problems linked to the health crisis.
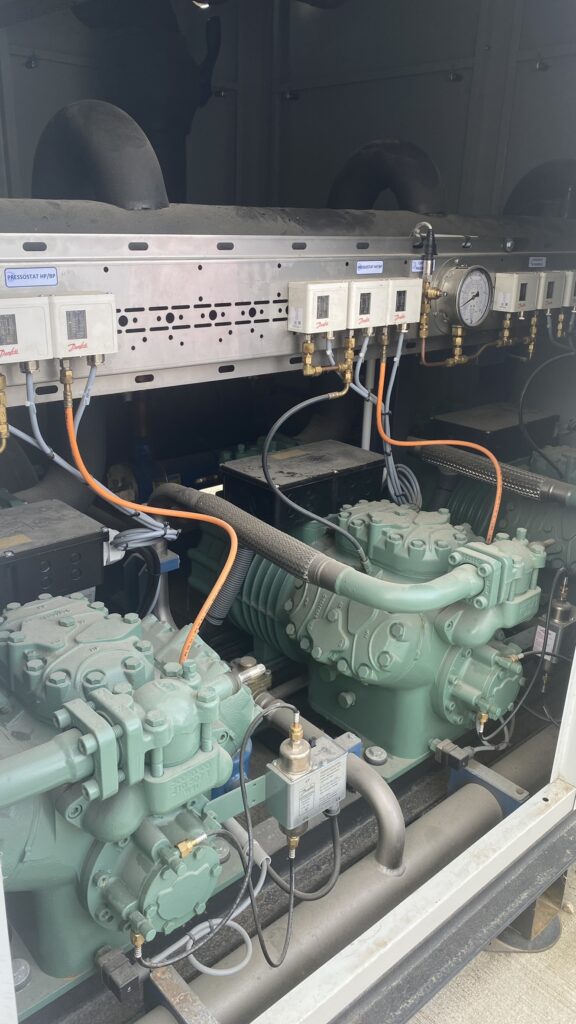
A Pecomark refrigeration system, consisting of 5 Bitzer 6FE-44Y compressors, the first of which had a variable speed, was charged with 260 kilos of R-1234ze. The heat recovered from the cooling system covered all the hot water process needs. The secondary network was charged with 11 m3 of Greenway® Neo N -18°C. The whole system supplies 20 independent workspaces with strict temperature and/or humidity management. The hydraulic pumps were also equipped with variable speed control to optimise the operation of the system and reduce energy consumption associated with two buffer tanks. New cubic, double flow and double coil GUNTER evaporators (with hot water coil for humidity management) were installed. 1,130 m of piping was laid for the cooling and 960 m for the heating.
Solstice® ze with a very low GWP has the advantage of having a very good coefficient of performance. Combined with Greenway® Neo N, an NSF HT1 registered bio-sourced heat transfer fluid, it is a winning combination in terms of sustainability.
The installation has been in operation since last September and all those involved are fully satisfied.
Installation of an indirect system with 340 kW cooling production

From left to right: Pierre Delpech, Head of the design office, Xavier Delzescaux, company director, Sarah Zioini, Climalife Key Account Manager.