In a sector where performance and efficiency are critical, it is essential to upgrade outdated equipment to ensure high quality production.
A major UK-based manufacturer specialising in the production of plastic bottles and tubes turned to Pitkin & Ruddock, refrigeration experts with over 70 years’ experience in the installation and maintenance of systems and temperature control.
Ross Richardson, Technical Sales and Projects Engineer, and Danny Gell, Pitkin & Ruddock Branch Director, recommended new chillers with a more environmentally friendly heat transfer fluid to help the plastics manufacturer meet its sustainability targets.
The project was launched to upgrade the refrigeration systems responsible for supplying a continuous flow of chilled water, essential for cooling the production moulds and solidifying plastic tubes and bottles. The system was designed with separate heat transfer fluid and water circuits.
In this context, the liquid coolers are located at the point where the plastic moulding takes place, with water loops integrated into the cooling process. The efficient operation and integration of these systems were essential to the success of the project.
Many challenges to overcome on this project

The first was to replace the outdated chillers and coordinate their phased removal, while installing the new ones with minimum disruption to the continuous flow of chilled water.
The second was to find space for the new chillers, which had to be strategically placed close to the production lines to reduce the distance to the chilled water network for greater operational efficiency.
The third and equally important challenge was to minimise downtime during the transition to ensure the plastic moulding process, vital to production, remained uninterrupted.
Pitkin & Ruddock then developed a phased approach to removing the old chillers and installing the new ones to ensure continuity of operations.
The final challenge was to choose the right heat transfer fluid. Rob Attawia, Regional Sales Manager at Climalife, and Neil Roberts, Technical Sales Director, recommend Greenway® Neo N, a safe and sustainable heat transfer fluid that met the end customer’s expectations. After studying the technical properties, Pitkin & Ruddock decided to innovate and select this solution formulated and produced by Climalife.
Greenway® Neo N based on 1,3-propanediol is bio-sourced. This renewable raw material offers a natural,reliable and efficient alternative to mono-propylene glycol (MPG) from the petrochemical industry. Its production reduces CO2 emissions by 84% compared with MPG and consumes 70% less non-renewable energy. The Greenway® Neo N safety data sheet has no pictograms, a significant advantage to consider when selecting a product for the safety of operators and equipment.
2000 litres of Greenway® Neo N was loaded into the system
Pitkin & Ruddock trusted the expert advise of the Climalife team for their first installation and the processes went very smoothly.
To replace the old units, dry coolers from Kelvion were selected to meet both operational requirements and the customer’s sustainability goals. Three Daikin liquid chillers were also installed and charged with 57 kg of R-32.
Since their introduction, the new chillers have offered a number of quantifiable benefits,improving operational efficiency and profitability for the plastics manufacturer. With better temperature control enabling more precise adjustments, product quality is improved. The advanced technology of the new chillers also means greater energy efficiency, with reduced energy consumption and an expected return on investment of three years. What’s more, these new chillers require less maintenance, freeing up valuable time and resources, and their longer lifespan also helps to reduce costs and promote more sustainable practices.
Building on this success, the manufacturer has decided to implement similar upgrades at another production site, further confirming the choice of Greenway® Neo N.
“We are pleased to report that the upgraded chillers in the end user’s facility have significantly improved energy efficiency and operational performance. The Greenway®Neo N has proven to be the best choice for this project,” said Ross Richardson.
Installation design :
- Chillers (liquid coolers):
- 3x Daikin EWAT430B-XLB200
- Refrigerant:
- R-32 – 57 kg charge
- Cooling capacity:
- 430 kW with Greenway® Neo N at 7ºC
- Dry Cooler model:
- Kelvion LV-LA208T5X-091R885
- Power: 950 kW
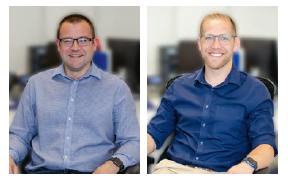