Staying ahead of F-Gas regulations
Environmental responsibility and innovation are an integral part of the group’s strategy. Constantly monitoring the market, the manufacturer is always on the lookout for a refrigerant that could meet future regulations and be suitable for its equipment. The manufacturer has been studying long-term refrigerant options, so that it can be ready for the 1st January 2022 deadline and has been using R-452A to replace R-404A as an interim solution. Hydrocarbons such as propane are quickly being removed from the specification due to the charge limit of 150g per system.Preventive measures for a compliant market launch
Having been approached by Climalife in 2017, experts began the widespread introduction of R-455A; an A2L fluid, explaining the challenges of this new classification and technology. Vauconsant then became interested in the thermodynamic characteristics of this refrigerant, and quickly realised that this HFO blend was likely to meet its expectations. In April 2018, the manufacturer launched a prototype in its test laboratory. Vauconsant; in partnership with compressor manufacturer Tecumseh, tested a standard chiller model and analysed its performance over a three-year period considering longevity and wear of components, motor bearings, oil, etc., to assess its reliability and compatibility. To comply with CE certification and prevent potential risks, the company wants to market its equipment using components that are 100% approved for R-455A by the manufacturers. In parallel, Vauconsant is planning ahead and implementing a system for charging A2L classified refrigerants in its factory. Although it is considered a mildly flammable refrigerant, safety protocol has been defined for charging the new refrigerant. Patrice Antoine, Technical Manager at VAUCONSANT explains: “An ATEX zone has been developed to enable R-455A cylinder charging from the end of July. An area of the workshop will be marked out with ventilation outlets to keep the gas at ground level in case of a leak, so that it can be easily evacuated. Installed leak detectors will operate at various levels, depending on the degree of urgency, to alert us accordingly.” No additional restrictions have been established for the plant. Internal training for the safety department and refrigeration workers has been scheduled to educate and raise awareness of rules governing the correct use of this type of refrigerant.R-455A: the fluid of the future for all Matfer Bourgeat Group subsidiaries
The manufacturer is pleased with the refrigerant’s low flammability, which allows refrigeration technicians to work under the same conditions as before and to handle it without problems. Its very low flammability excludes the risk of explosion, whether in storage at the factory or at the end customer’s premises. R-455A will be the standard specification from September 2021 for all custom-made equipment with charges of up to 2.5 kg per system. PI Création; is a manufacturer of made-to-measure equipment for very high-end kitchens that belongs to the same group. It has also decided to switch its entire range over to this new A2L refrigerant soon.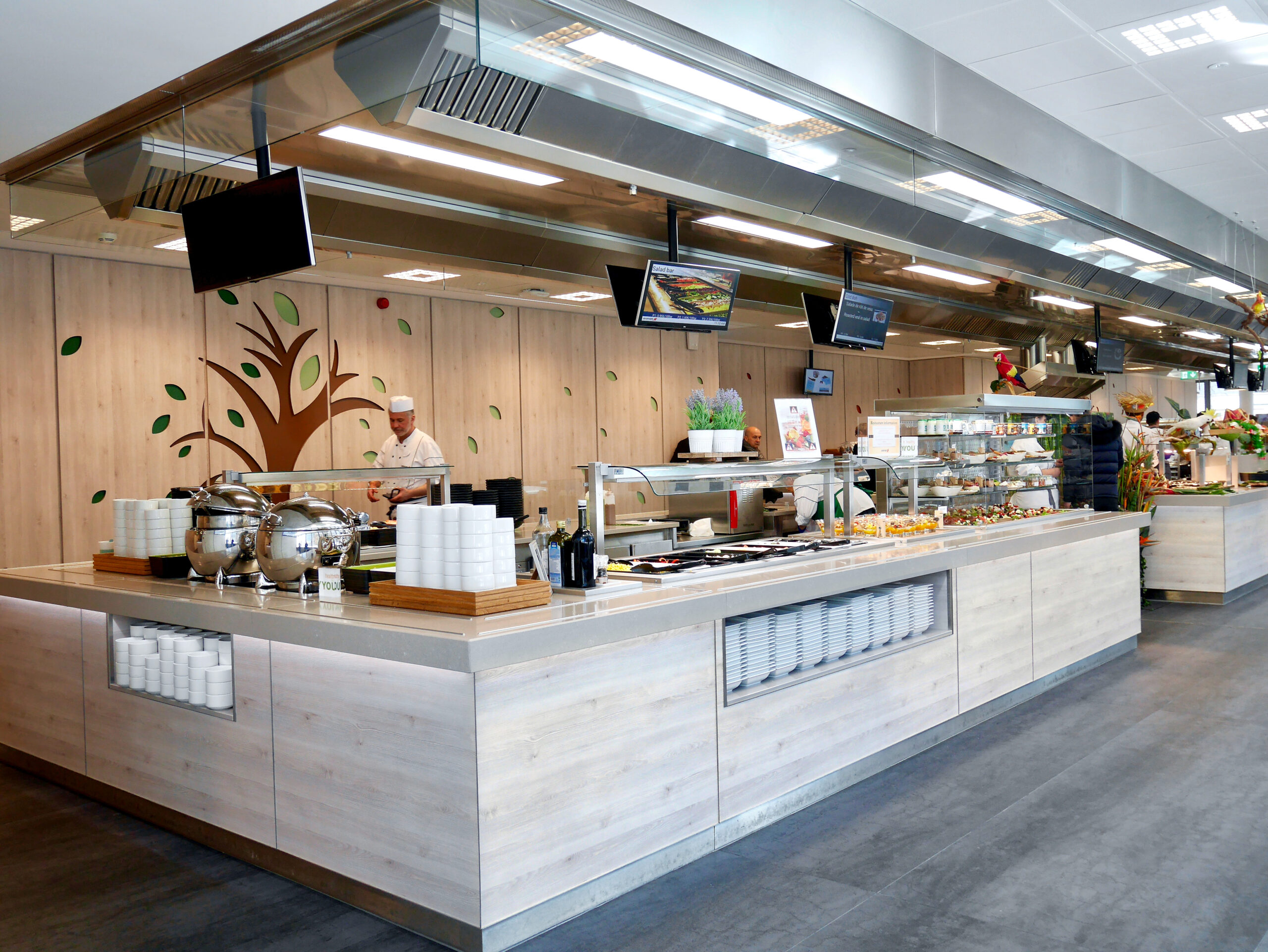
Characteristics of the refrigeration units used according to the project configuration:
Tecumseh unit with expansion valve: CAJ4513PHR Tecumseh unit with capillary tube: AE4425PH Evaporating temperature: -12°C Condensing temperature: +45°C In terms of system performance, better temperature regulation is observed. The compressor stops much less often, and there is more inertia at standstill. The fact that the temperature rises less quickly and the compressor restarts later even leads to significant energy savings. “The performance aspect has been a pleasant surprise for us. It reinforces the commercial discussions that we held early on about managing this transition. We were hoping not to lose too much ground compared to what was or expected at the start. The results were even better than we had imagined for the client: it’s a bonus all the way!,” says Bertrand Dugardin. All in all, it promises to be a smooth launch and commissioning. For Vauconsant, R-455A is undoubtedly integrated into the development of future equipment. A last objective is to be able to use smaller cooling units to create even more design-oriented equipment.“ Our transition has been guided by a reasonable decision that met regulatory requirements and ensured the safety of our employees, our customers and the end customer. ” concludes Bertrand Dugardin, Communications Manager at Vauconsant
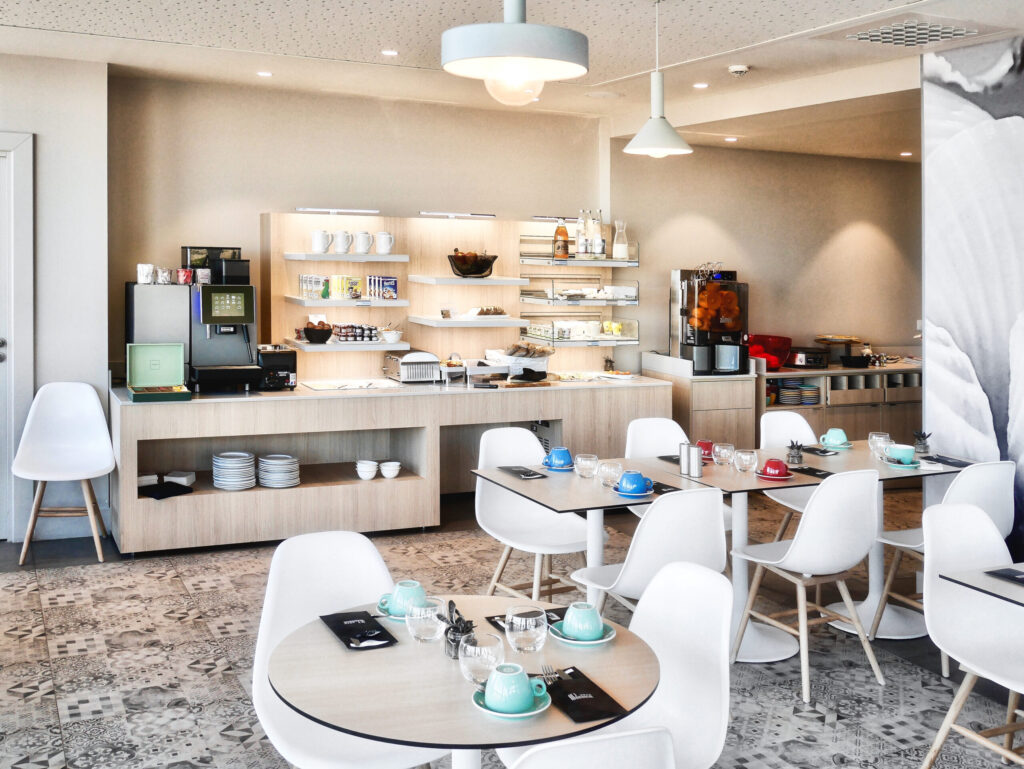
To reduce energy consumption, the company plans to adopt more of a “closed loop” work approach by providing even more autonomous equipment with heat recovery. Suppliers are making slow progress because the issue still involves significant cost.
For Vauconsant, R-455A is undoubtedly integrated into the development of future equipment. A last objective is to be able to use smaller cooling units to create even more design-oriented equipment.
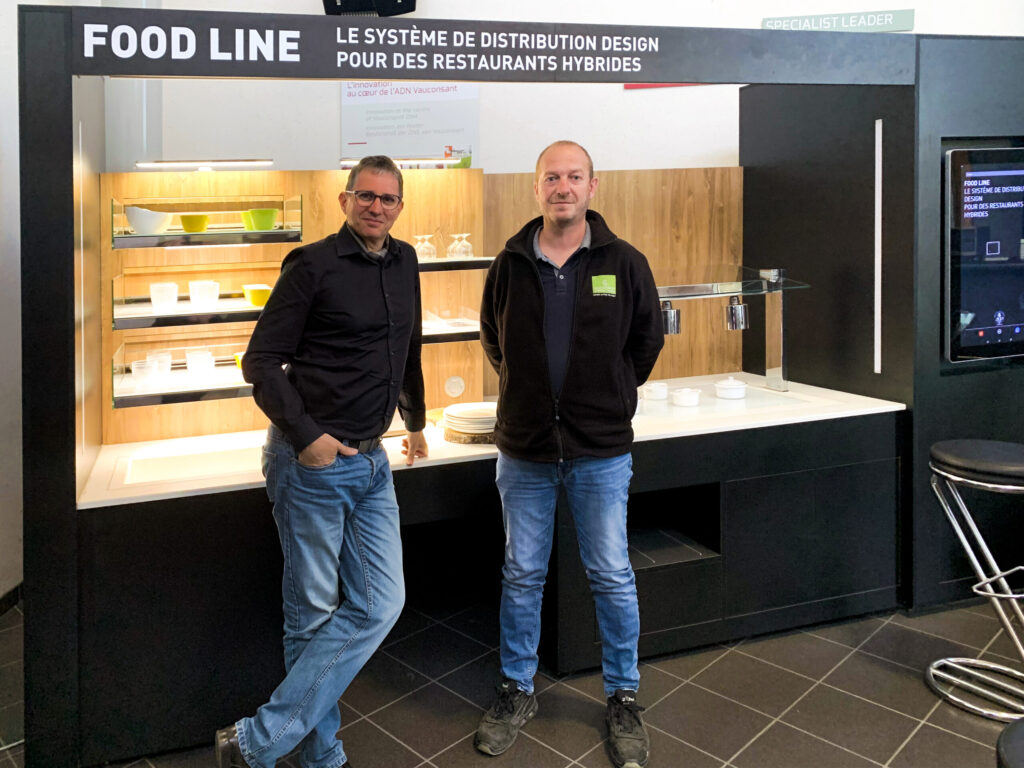
VAUCONSANT
- Sectors of activity : Design & manufacture of food distribution equipment
- Location : Lorraine, France
- Year founded : 1926
- 130 employees
- 2020 turnover : €15 million